珠江潮涌处,智造新高地。3月19日,在粤港澳大湾区,中铁宝桥参建的狮子洋通道狮子洋大桥东索塔首道钢横梁成功架设,标志着这座集五项世界第一于一身的超级工程,正以新质生产力重塑现代桥梁建造范式。
中铁宝桥集团党委书记、董事长李宗民在现场听取了项目进展汇报,并见证了这一重要历史时刻。他强调,狮子洋大桥是展现中国桥梁建造实力的重要窗口,要深入推进智能制造,加快发展新质生产力,以最高标准确保工程质量和安全,以技术创新为世界桥梁书写新篇章。
作为展现中国高端制造实力的战略工程,狮子洋大桥主跨2180米的双层钢桁悬索桥设计,对建造精度提出了极致要求。中铁宝桥集团承接狮子洋通道工程G2合同段主塔钢壳及锚固系统的制造任务,主要包括主塔钢壳、钢横梁及相关附属设施、锚碇锚固系统,用钢量约2.95万吨,其创新实践生动诠释了新质生产力的核心内涵。
精准把控精度
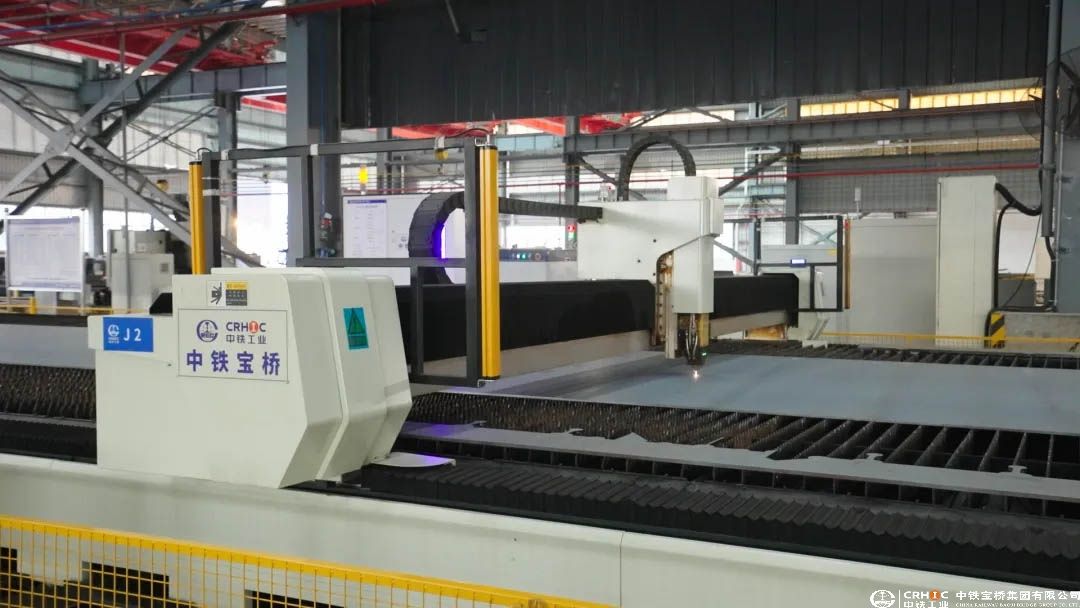
针对主塔钢壳节段壁板薄、加劲肋及附属件多、焊接量大等技术难题,采用了先进的数控激光下料和激光划线技术,显著提高了零件制作的精度,有效减少了结构变形。
创新性地制作了板单元专用反变形胎架,提前预设焊接反变形量,并在胎架四周进行适当约束,成功控制了焊接过程中的变形问题,确保了钢壳节段的高精度制造。
智能制造设备
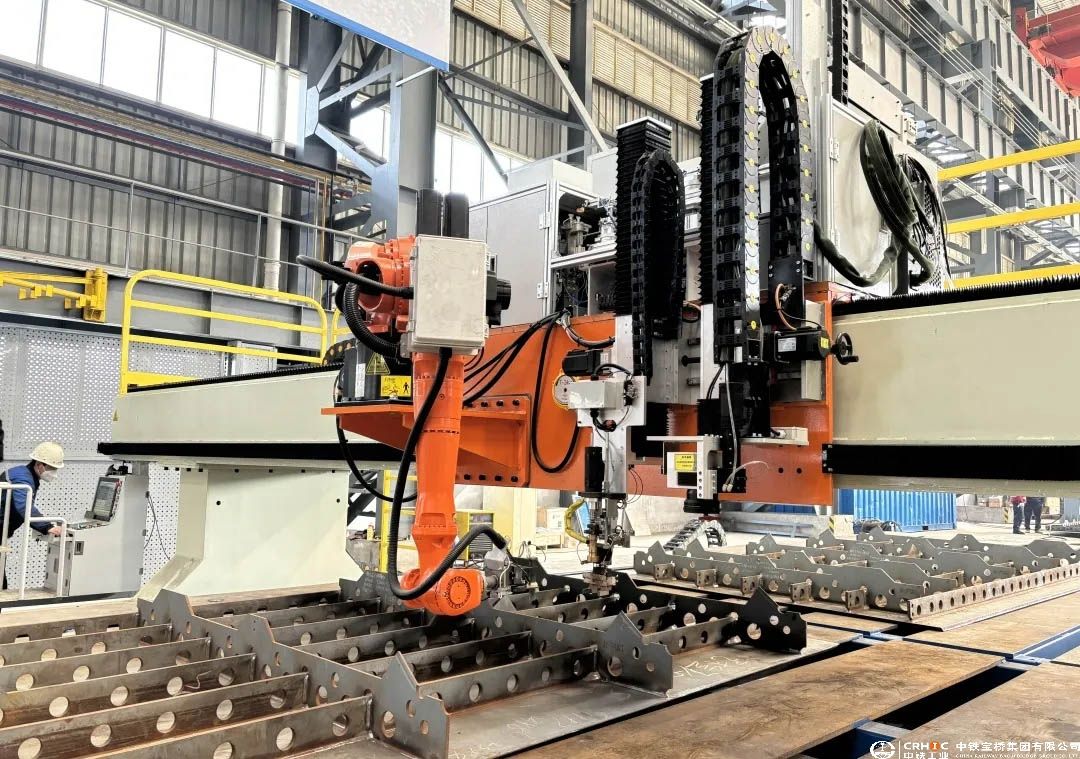
在主塔钢壳板单元的智能化制造过程中,中铁宝桥集团引入了自动组装定位焊机、板单元多电极焊接机器人、横隔板智能焊接机器人、剪力钉焊接机器人等先进设备。
这些智能化焊接设备的应用,大幅提升焊接质量和效率,减少人为因素对焊接质量影响,确保焊接作业的稳定性和可靠性,为大桥的长期安全运营奠定了坚实基础。
数字预拼技术
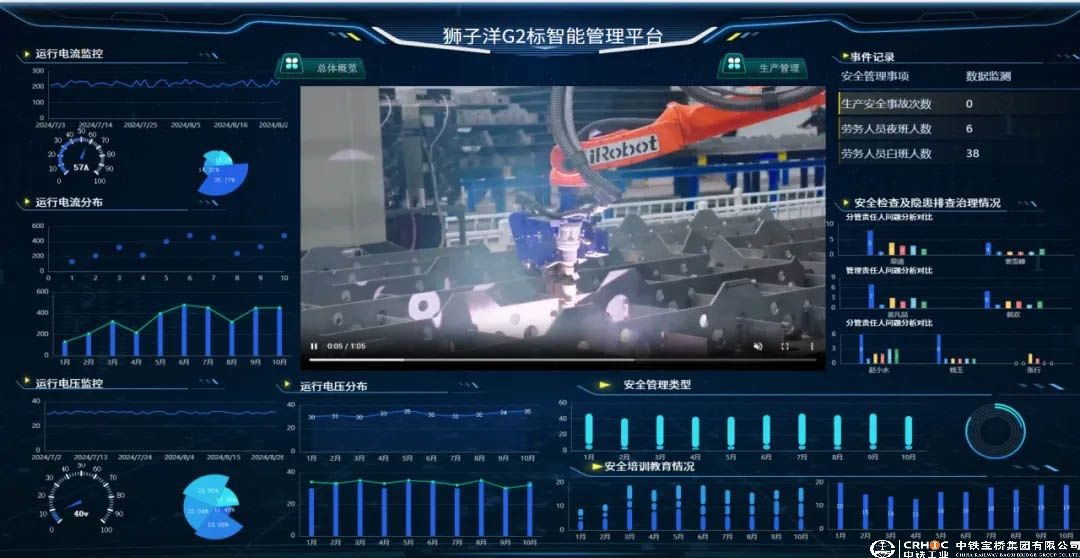
此次成功架设的首道横梁是大桥悬索系统的重要承力节点,也是整个东主塔六根横梁中唯一一根位于桥面下方的横梁,承担着极其关键的承重作用。横梁本身重量超过1200吨,由7个节段组成,加工和安装难度极高。
中铁宝桥集团利用BIM三维建模技术,实现了杆件的数字化预拼装。通过将横梁与钢塔壳进行三维建模,并在电脑中模拟现场拼装全过程,精准确定了安装位置,极大提高了现场安装精度,确保了横梁的精准对接。
该项目的创新实践验证了:在新一代信息技术与先进制造深度融合的背景下,传统基建行业正加速向“技术密集型+知识密集型”转型升级。狮子洋大桥的建设过程,实质是新质生产力要素在交通基建领域的系统性重构,其经验将为我国“新基建”高质量发展提供参考。
狮子洋通道是珠江口首条东西向双层过江通道,起于广州市南沙区大岗镇,终于东莞市虎门镇,路线全长约35公里。狮子洋大桥作为项目的关键控制性工程,采用双层钢桁悬索桥方案,实现了“一跨过江”的设计理念。大桥主跨长2180米,主塔为门塔式结构,高342米,相当于110层楼高,是世界最高的双层悬索桥主塔。建成后,将创造双层悬索桥“主跨跨径、主塔塔高、锚碇基础、主缆规模、车道数量”五项世界第一,成为全球桥梁建设史上的又一奇迹。